The Company manages occupational health and safety issues in accordance with the laws of the Republic of Kazakhstan and international standards for occupational health, safety, and hygiene. KMG has a proactive policy to protect its employees’ health and wellness, irrespective of the production process.
The number of non-injury-related deaths among employees of SDEs decreased by 5 cases, or 33 %, compared to 2021. The increase in these figures was mainly due to the presence of cardiovascular disease among employees.
KMG Personnel Health Management Program
As part of the implementation of Strategic Initiative 24 “Personnel Health Management”, the KMG Group Personnel Health Management Program was approved by the KMG Management Board on 23 December 2022 (Minutes No. 68). The aim of the Program is to improve the quality of medical care and medical services at production facilities, and to introduce and implement measures to improve the health of employees within KMG Group.
The main objectives of KMG Personnel Health Management Program are:
- Improving the quality of medical care and medical services to employees of KMG Group’s production facilities;
- Developing the mechanisms to strengthen personnel engagement and motivation for healthy lifestyle;
- Improving working, leisure and living conditions for employees of KMG Group’s production facilities.
Approval of the KMG Group Personnel Health Management Action Plan 2023–2025 is planned for 2023.
Number of non-injury-related deaths
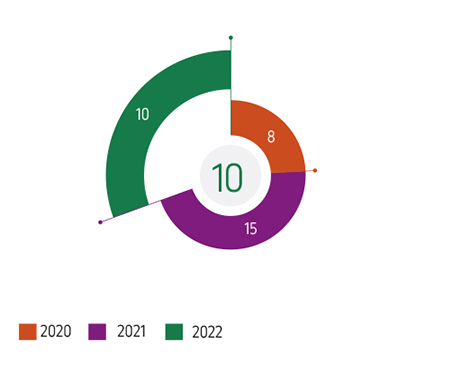
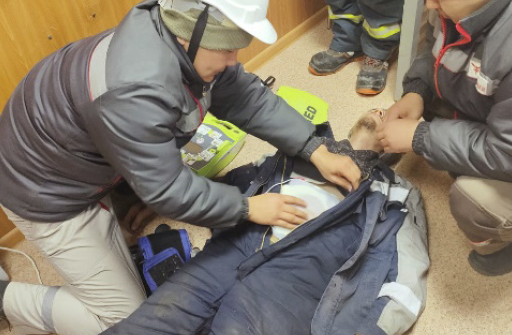
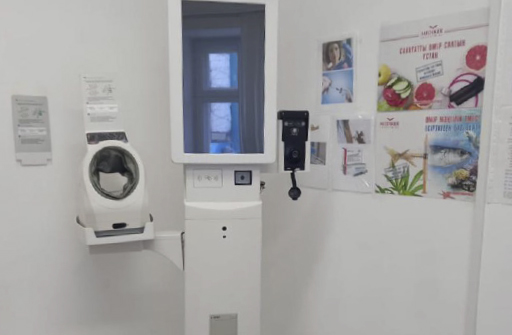
Electronic Health Checkup System
Starting from 2021, the Electronic Health Checkup System (EHCS) has been implemented in SDEs. The system simplifies and automates the process of examining the health of employees during health checkups. Within 5 minutes, the EHCS hardware system can analyze 10 key health parameters of an employee and issue a report or a travel voucher. If the EHCS hardware system detects any abnormalities in the employee’s health, he or she will be referred to a doctor for examination.
Currently, EHCS hardware systems have been implemented at EMG, KTO, AR and PPCP.
The automation of health checkups avoids shortcomings and speeds up the procedure of health checkups and the impartiality of the results of health checkups.
One important problem is the study of the combined effect of industrial health hazards in production conditions and joint exposure (e.g., microclimate, noise, vibration, aerosols, work stress, etc.), the prediction of the effects of their action, as well as the study of the development of occupational pathology.
Along with this, prolonged consumption of unbalanced nutrition in conditions of exposure to environmental factors in the workplace is an additional cause of the development of the pathological process. Therefore, in the general complex of measures to prevent the adverse effects on the body of harmful factors of the production environment, an important role should belong to the organization of quality nutrition.
It should be noted that the energy requirements for employees of subsidiaries engaged in heavy physical labor should be at least 3,700-3,850 kcal.
Based on the analysis of data submitted by SDEs on the diet and range of food products at the catering facilities for organizations providing catering services to SDEs’ employees, the following measures for improvement are being implemented:
- appropriate diet in terms of protein, fat, carbohydrate, calories and vitamin content;
- correct indication of the energy value (calorie content) of food products;
- avoiding the repetition of the menu with the same meals both in the next 2 calendar days and over a period of 5 days;
- inclusion of such foods as fish, animal liver, fruit and berries, herbs, nuts and seeds, bran, vegetable oils and fibre in the diet;
- providing a nutritionally balanced diet;
- providing preventive nutrition in the menu for workers with chronic diseases.
Medical Emergency Drills
In accordance with the KMG Group Emergency Medical Care Regulations and the Medical Emergency Response Plan, SDEs are tested annually and on a regular basis at each production facility by holding medical emergency drills. For example, at Atyrau Refinery LLP’s process facilities, 12 medical emergency drills were held in 2022, six of which were held with the participation of contractors located at the refinery site. Medical emergency drills were held on the following topics: first aid in case of a fall from a height, unconsciousness, poisoning, cardiac arrest, etc. Reports were drawn up for each medical emergency drill held, taking into account the non-compliances identified.
No cases of non-compliance in the area of impact of products and services on employees’ health and consumer safety have been reported in KMG Group in 2022.
No occupational diseases have been reported in KMG Group.